Alumina ceramic foam filter is also called ceramic foam filter plate, or aluminum casting filter. It can effectively remove the inclusions in the aluminum liquid, and absorb the micro-sized fine inclusion particles. Ceramic filter plates play an important role in the production of the aluminum alloy casting industry. It can improve surface quality, product performance, and microstructure, and improve the yield of aluminum.
Since 2012, AdTech company has been focusing on the research and development of highly absorbent alumina ceramic foam filter plates. Now, the technology of ceramic filters has been mature, and it is widely accepted in the market. Ceramic foam filters are suitable for the filtration and purification of multiple series of aluminum alloy products, such as micron aluminum foil, PS board base for printing, flexible packaging materials, rail transportation, aerospace products, electrical cables, wires, etc.
Filter-alu

Ceramic Foam Filter is a kind of high-absorption ceramic filter plate. It is between in the filter bowl for filtering impurities in molten aluminum alloy. Ceramic filters can meet the requirement of production in high-tech performance aluminum alloy.
Learn MoreFilter-PAl
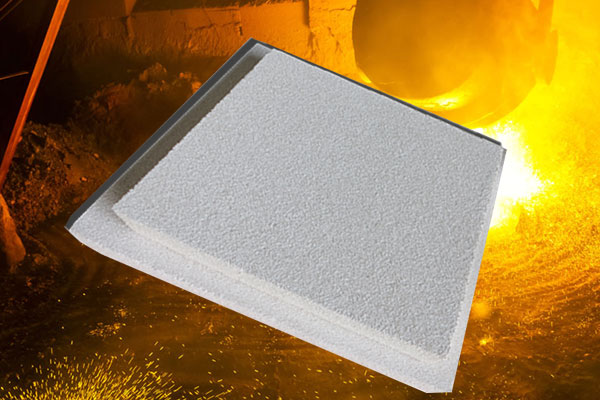
AdTech ceramic foam filter -PAl takes reticular structure and organic foam as a carrier. Put it into the Al2O3 slurry, and the slurry evenly deposits in foam. After drying solidification, the carrier will turn into the final product under 1180°C. The ceramic filter is especially used for aluminum precision casting.
Learn MoreCeramic Foam Filter Dimension
660x660x50(26″)
584x584x50(23″)
508x508x50(20″)
432x432x50(17″)
381x381x50(15″)
305x305x50(12″)
228x228x50(9″)
178x178x50(7″)
Ceramic foam filter Pore Size(PPI):10/20/30/40/50/60
30ppi 40ppi Foundry Filter is the most commonly used ceramic foam filter in the aluminum casting industry.
Ordinary aluminum casting usually uses 10-40ppi ceramic filter plates.
Aviation and high-quality aluminum materials usually use 30-60ppi ceramic filter plates.
Alumina Ceramic Foam Filter Advantages
- Adopt the principle of adsorption to filter. Alumina ceramic foam filter can effectively remove large inclusions in aluminum liquid, and effectively adsorb fine inclusions of micron size. It has high filtration accuracy at the same mesh size.
- Do not drop slag, effectively reduce the pollution to aluminum liquid.
- Good thermal shock resistance and corrosion resistance to molten metal.
- Automated assembly line production, three calibration procedures, precise dimensions, and more suitable for the filter box.
- Improve surface quality, product performance, and microstructure.
Production Process
AdTech alumina foam ceramic filter plate uses organic foam as a carrier. These organic foams have a three-dimensional network structure. Put the foam carrier into a special ceramic slurry with thixotropic properties. Then the technician uses a special roller extrusion process, making the ceramic slurry uniformly coat on the carrier. After drying and curing, the final ceramic filter plate is fired at high temperatures. There are sealing linings around the ceramic filter plate. It is mainly used for the contact surface between the filter plate and the filter box to prevent the leakage of liquid aluminum through the contact surface. AdTech ceramic foam filter adopts three kinds of sealing gaskets of different materials: fiber paper, fiber cotton, and expanded cotton.
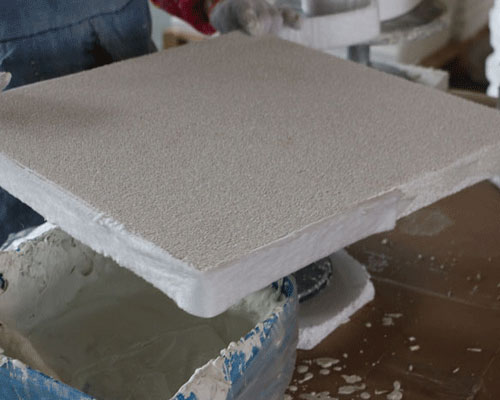
How to Use Ceramic Filter Plate
-
- Clean the plate-type filtering box.
- Put the ceramic foam filter plate into the filtering box gently. Then press the sealing gasket around the filter plate by hand. To prevent the aluminum liquid from flowing sideways.
- Preheat the filter box and filter plate evenly. To make the temperature close to the temperature of molten aluminum. Pre-heating can remove moisture and facilitate instant filtration immediately. The preheating method can adopt electric or gas heating. Usually, preheating takes about 15-30 minutes.
- Pay attention to the aluminum hydraulic head during casting. The normal initial head is 100-150㎜. When the molten aluminum begins to pass, the head will drop below 75-100mm. And then the head will gradually increase.
- During the normal filtering process, avoid knocking and vibrating the filter plate. At the same time, the aluminum liquid should be full in the flow tank, to avoid too much disturbance.
- After filtering, remove the filter plate in time, and clean the filter box.