Degassing Unit
The aluminum degassing unit adopts new high silicon melting material manufacturing technology. The main components include a mechanical drive, box lid, rotor, and heater. AdTech degassing equipment can meet the production of aluminum products with high technical performance requirements. Aluminum degassing machine is between the furnace and the casting machine, the main function is removing hydrogen and other residues. Otherwise, these gases will affect the quality and mechanical properties of aluminum and its alloys.
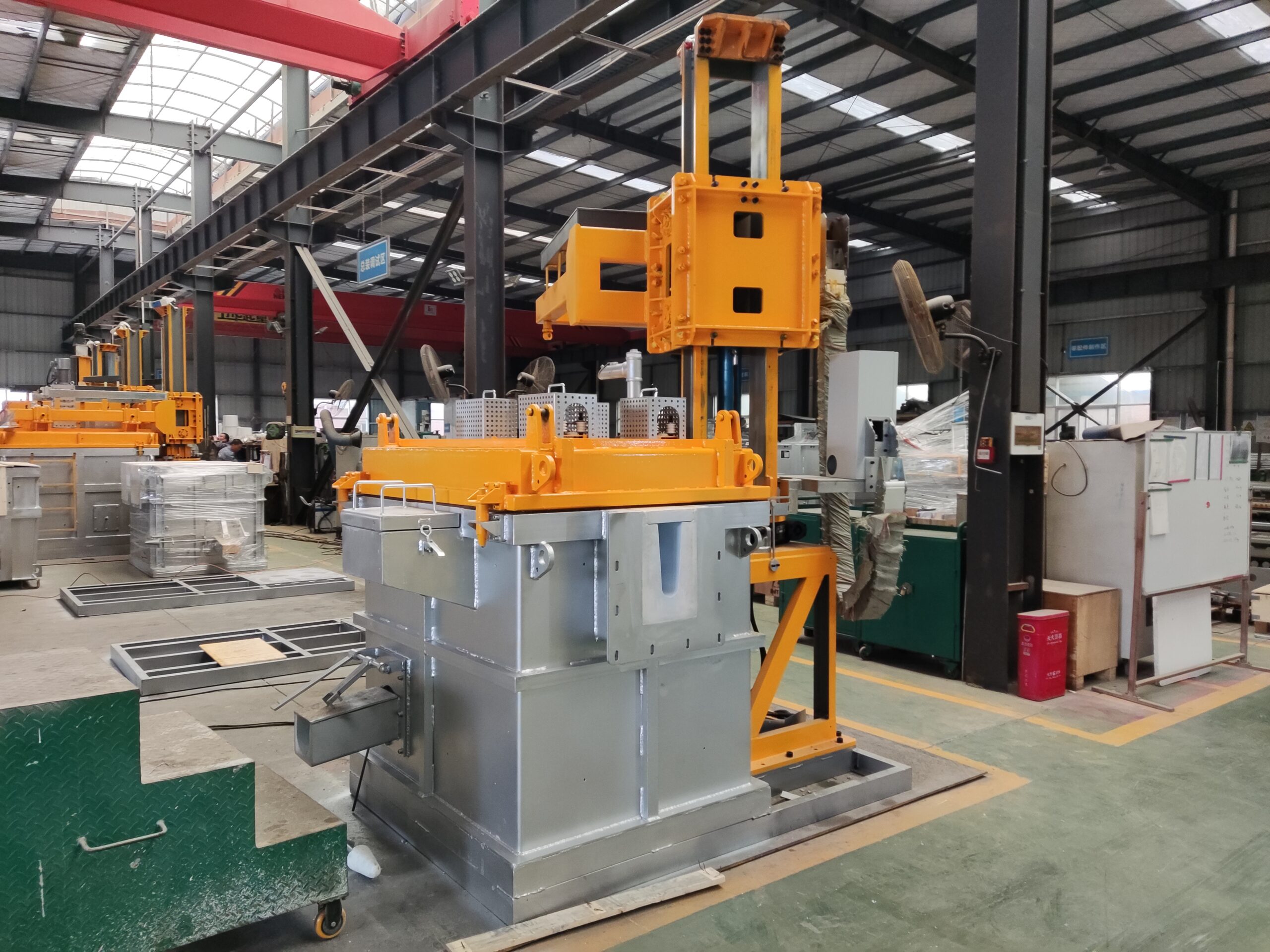
Parameters of Online Degassing Unit
Max Degassing flow MT/H |
15 MT/H | 35 MT/H | 65 MT/H |
---|---|---|---|
Degassing Box Standard | 1 room 1 rotor (1B1R) | 2 rooms 2 rotors(2B2R) | 3 rooms 3 rotors(3B3R) |
Degassing box structure | 1 draining outlet & 1 deslagging outlet | 2 draining outlet & 1 deslagging outlet | 3 draining outlet 1 deslagging outlet |
Lifting System | Hoisting type | Rotor mechanical lifting | cover hydraulic lifting |
Features of Rotary Degassing Machine
- Good degassing effect: The average degassing efficiency is 60%.
- The inner lining is made of high-silicon molten material. It has a long service life. The non-stick aluminum effect is good, with no pollution from molten aluminum. The spoiler of the inner lining can prevent air and oxides from entering into the liquid aluminum.
- The rotor is made of silicon nitride. It has strong advantages in corrosion resistance, thermal shock resistance, oxidation resistance, wear resistance, mechanical strength, and others. The rotor can diffuse the bubble to all corners of the inner cavity to the maximum extent.
- Immersion heater protective sleeve is made of silicon nitride. The heating efficiency is high. It can reduce the oxidation of the aluminum and have no pollution to the molten aluminum.
- The degassing device can use a mixture of argon, nitrogen, and chlorine as an option. There are protection measures for using these gases.
- The standard seal structure design can effectively prevent slagging from secondary oxidation, and improve the degassing effect.
Working Principle
Place a molten aluminum degassing machine between the holding furnace and the casting machine. Blow the Nitrogen into the molten aluminum alloy, and the gas is shredded by the rotating graphite rotor in the degassing tank. Then a large number of dispersed bubbles are formed, so that the liquid aluminum alloy is in full contact with nitrogen in the treatment tank. According to the air pressure difference and the principle of surface adsorption, bubbles absorb hydrogen and oxidized slag. And then the bubbles rise to the surface of the melt to form scum. Then molten aluminum alloy flows from the outlet of the degassing unit to the casting machine. The liquid aluminum alloy continuously enters the degassing device, and nitrogen is continuously blown in. With such a purification process, the degassing machine can achieve the purpose of purifying the aluminum alloy.
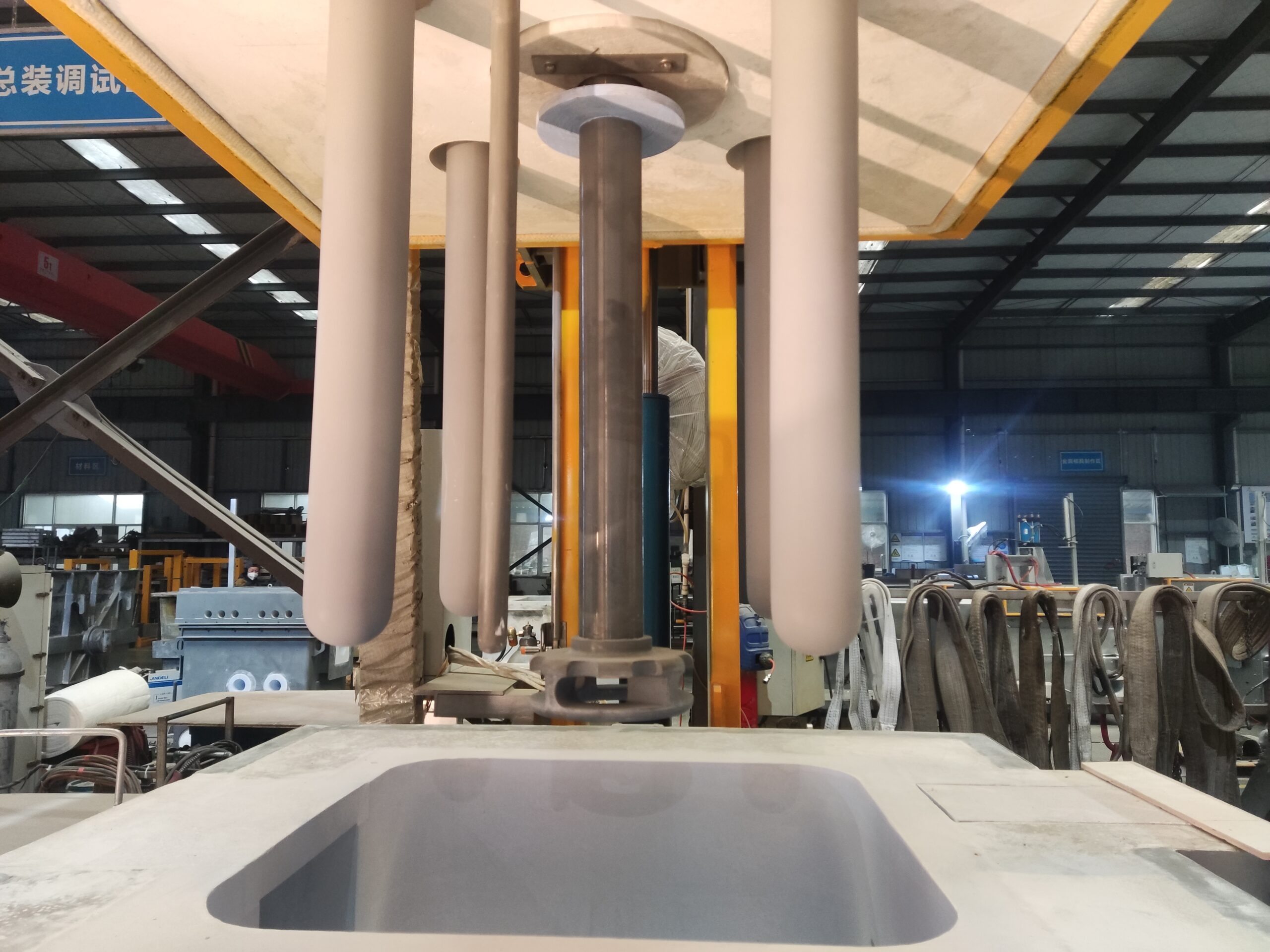
Structure of Degassing Device
The online degassing unit includes a processing box, lifting system, heating system, graphite rotor, and control system.
1. Processing Box
The processing box includes the decontamination chamber and heating and insulation room. The middle is separated by a SiC material partition, and the bottoms of the two chambers are connected. After degassing and slagging in the cleanroom, the molten aluminum alloy flows into the heat preservation room from below the partition. The heat preservation room adopts a U-shaped silicon-carbon holding jacket silicon carbide protective tube, immerses it in liquid aluminum alloy and heat. The outer shell of the box body adopts a steel plate, and the inner lining uses refractory material. The upper part of the sidewall sets an observation and inspection slag port, and the bottom sets a slag port.
2. Lifting System
Use two hydraulic cylinders as the lifting device, which can control the movement of the graphite rotor and the U-shaped silicon carbon rod heater. They can rotate 90 ° horizontally, the hydraulic system is relatively stable, and the positioning is accurate.
3. Heating System
The heating system uses an immersion heater and silicon nitride protection tube. There is a temperature-measuring thermocouple in the tube, which can realize automatic temperature control. The temperature control system uses a more advanced power-integrated unit.
4. Graphite Rotor
The graphite rotor rotating nozzle adopts high-purity graphite. The frequency converter can control the speed of the graphite rotor. The high-purity oxidation-resistant graphite rotor has the characteristics of high strength, high-temperature resistance, and corrosion resistance.
5. Control System
The control system consists of two parts: a gas control cabinet and an electric control cabinet. Gas control includes nitrogen and compressed air control, equipped with manual/automatic control. The electronic control part mainly includes transmission control and temperature control.
Degassing Process
Before the molten aluminum enters the degassing equipment, the worker should switch off the heating element. When the temperature of the heater is close to the molten aluminum. Inject the inert gas into the rotor, and then fill the molten aluminum into the degassing box.
Note
- Check the sealing material at the connection between the inlet, outlet, and flow cell.
- Check whether the temperature of the molten aluminum is high enough. Stop filling work when the level is approximately 3 cm from the bottom of the tank.
- The operator must wear an appropriate protective jacket. When the metal flows into the box, it will produce scum. Workers can clean the metal surface scum in the slag mouth.
- During the heat preservation phase, the aluminum liquid is allowed to remain in the cabinet at a set temperature.
- Inject a small amount of inert gas into the rotor, to prevent the liquid aluminum from entering the rotor and block the air outlet.
- Start the heater immediately after the filling of the molten metal has stopped.