bn coating high and stable quality, the following content revolves around this center.
The test alloy is T1-50% (atomic fraction, the same as the shape memory alloy below) provided by Beijing Nonferrous Metals Research Institute
The interface reaction test between the shell and the T-alloy was carried out in a self-made vacuum induction heating furnace: the Ti-alloy was heated in a calcium oxide crucible, and the induction furnace was evacuated to 7Pa. To avoid the discharge of the induction coil, the furnace was filled with high-pressure Pure argon protection. The casting temperature of the alloy is 1470 ℃ and 1600 ℃ respectively, and it is taken out when the casting temperature is lowered to room temperature. To study the reaction layer on the surface of the casting, the casting was not treated by shot peening and pickling, but only the mold shell was cleaned and then sampled by wire cutting.
Samples were histologically analyzed using an S-570 scanning electron microscope with attached EDS and a JAX-8100 electron probe.
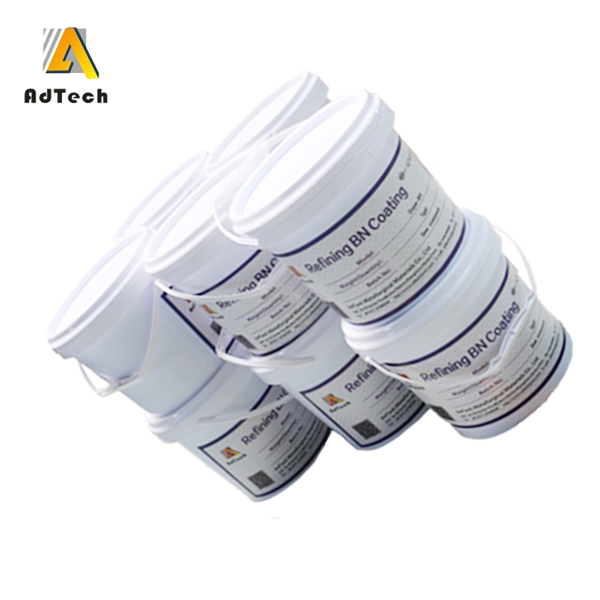
1 Test results and discussion
1.1 Analysis of the reaction interface between the bn coating-based composite shell and the titanium-nickel alloy The melting point of the T1
-50%N shape memory alloy is 1321 ℃. In this experiment, T1-50%1 shape memory alloy samples were prepared in bn coating-based composite molds at casting temperatures of 1470 and 1600 °C, respectively. Figure 1 is a low-magnification photograph of titanium-nickel alloy castings prepared from bn coating-based composite molds at different casting temperatures. It can be seen that at the normal casting temperature of 1470 °C, the surface of the titanium-nickel alloy casting prepared by the bn coating-based composite mold is smooth, and there is no sand sticking phenomenon, as shown in Figure 1(a). This shows that the bn coating-based composite shell has good resistance to thermal shock and molten metal erosion, can withstand the erosion of high-temperature titanium alloy melt, and shows good remodeling ability. To investigate the reaction between the bn coating-based composite shell and the titanium-nickel alloy under extreme overheating, the casting temperature was increased to 600 ℃.
Figure 2 is a scanning electron microscope photograph of vertical cross-sections of titanium-nickel castings cast in bn coating high and stable quality-based composite molds by wire cutting at different casting temperatures. It can be seen from the figure that irregular titanium alloy phases are distributed on the matrix of the samples prepared at different temperatures, and the titanium-nickel castings have good compactness without obvious pores and shrinkage porosity. There are no large particle inclusions in the casting (the particle size of Y2O3 in the coating high and stable quality-based composite shell surface layer is greater than 36m, the particle size of BN is greater than 30um, and the particle size of yttrium oxide for sanding is greater than 120um), indicating that then coating-based composite mold The shell has very good refractoriness. At 1470°C, the bn coating high and stable quality-based composite mold and the titanium alloy melt hardly react. Even under the scouring of the titanium-nickel alloy melt at 1600 ℃, the problem of peeling and particle peeling did not occur. Therefore, when the bn coating-based composite mold is used in the titanium-nickel alloy, it can not only ensure the shape of the mold but also ensure the purity of the alloy casting.