Aluminum alloy smelting and pouring are the main links in molten aluminum casting production. The strict control of the entire process of melting and pouring plays an important role in molten aluminum casting defects. Since the aluminum melt has a large tendency to absorb hydrogen, the oxidation ability is strong. Precautions must be taken during the melting and molten aluminum casting process to obtain high-quality castings.
Raw Material Control
In order to melt high-quality aluminum melt, qualified raw materials should be selected first. The raw materials must be scientifically managed and properly handled. Otherwise, it will seriously affect the quality of the alloy. The charge should be sand-blasted before use to remove surface rust, grease and other contaminants. All the charges should be preheated before entering the furnace to remove the moisture attached to the surface and shorten the melting time to more than 3 hours.
Preparation of Hot Top Casting Parts
New crucibles and old crucibles that have not been used for a long time, should be sand-blasted before use and heated to 700-800 degrees for 2-4 hours. In order to burn off the water and combustible substances attached to the inner wall of the crucible, when it is cooled below 300 degrees, carefully clean the inner wall of the crucible, and spray the paint when the temperature is not less than 200 degrees.
Hot top casting parts should be preheated before use, and coated with protective paint at a temperature of 150 degrees-200 degrees, and thoroughly dried. After use, the oxides and fluorides attached to the surface should be thoroughly removed.
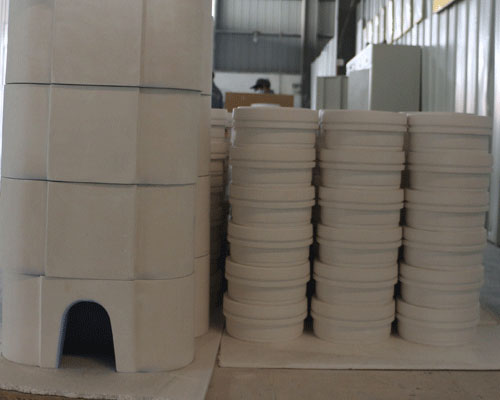
Melting Temperature Control
The smelting temperature is too low, which is not conducive to the dissolution of alloy elements and the discharge of gases and inclusions. In addition, due to the insufficient heat of the riser, the molten aluminum castings cannot be reasonably compensated. Excessive smelting temperature is not only a waste of energy, it is more serious because the higher the temperature, the more hydrogen absorption, the coarser the crystal grains, the more serious the oxidation of aluminum.
Melting Time
In order to reduce the oxidation and gettering of the aluminum melt, the residence time of the aluminum melt in the furnace should be shortened as much as possible and the smelting should be rapid. From the beginning of melting to the completion of pouring, the sand Molten Aluminum casting should not exceed 4 hours, the metal casting should not exceed 6 hours, and the die casting should not exceed 8 hours.
Transfer Molten Aluminum
Although the density of solid alumina is similar to the density of aluminum melt, after entering the aluminum melt, it will take a long enough time to sink to the bottom of the crucible. The aluminum oxide film formed after the aluminum melt is oxidized, but only the side in contact with the aluminum melt is dense, and the side in contact with the air is loose and has a large number of small holes with a diameter of 60–100A. It has a large surface area and strong adsorption. It is easily adsorbed on water vapor and has a tendency to float up.
Therefore, the difference between the specific gravity of this oxide film and the aluminum melt is small, and it is mixed into the melt, the floating speed is very slow, it is difficult to exclude from the melt, and the formation of pores in the molten aluminum casting is too mixed. Therefore, the key to transferring aluminum melt is to minimize the stirring of the molten metal and minimize the contact between the melt and the air.
Pouring Molten Aluminum
When using the tilting crucible to transfer the melt, in order to avoid mixing of the melt and the air, the ladle should be placed as close as possible to the furnace nozzle and placed at an angle. Make the melt flow down along the sidewall of the ladle, so as not to directly impact the bottom of the ladle, causing agitation and splashing.