Regarding”ceramic foam filters for casting“, there are the following common methods:
1. Freeze-drying
The full name of the drying method is vacuum freeze drying, which was invented by the British Wollaston in 1813. The principle of freeze-drying is to freeze the material to be dried at a low temperature to below its eutectic point so that the moisture in the material becomes solid ice, and then in a suitable vacuum environment, the ice is directly sublimated into water vapor by heating. and removed to obtain a dry product. At present, people have applied the freezing principle to prepare porous ceramics. For example, Bechtold and Mahler reported a freeze-forming process for ceramic fibers that used a phase separation technique for colloidal hydrates such as silicic acid. In this process, the columnar gel is surrounded and isolated by ice, and the growth direction of the ice in the solution is controlled to be unidirectional growth, and the fibers are formed after the ice melts. In another freeze-drying process for preparing porous ceramics, the solvent is directly sublimated from the solid state to the gaseous state, and the porous ceramics with good orientation and high porosity (>90vol%) are obtained by controlling the freezing direction of the metal salt solution. ceramics.
2. Template method
The template method is a technology that can precisely control the pore structure, pore size, and distribution. Currently, there are mainly the following approaches: (1) Porous body-in situ reaction method: the most typical is porous SiC. Porous carbon is first prepared, and then silicified Porous SiC is formed. Aoki directly reacts to silicon gas with porous carbon to prepare porous SiC that maintains the shape of porous carbon. Zhang et al. prepared unidirectionally arranged porous AlO3 by dipping cotton threads into the slurry, with a bending strength of 155±20MPa, a pore size of 165μm, and a porosity of 35wol%. ②Polymer template method: The core-shell structure with the ceramic as the shell and the polymer as the core is used as the template, and the polymer is removed by calcination to form a porous ceramic. The polymer template method is a new technology for the preparation of porous ceramics. It uses the colloidal flocculation method to produce a core-shell structure with the polymer as the core and the ceramic as the shell. Tang’s prepared polymethyl methacrylate polymer spheres with a monodisperse particle size of several hundred nanometers as templates, and ceramic nanoparticles (AlO3, TO2, and zrO2) modified by polypropyleneimide as ceramic materials. Polymer/ceramic core-shell composites are satin fired into nanoscale porous ceramics with controllable pore size. Among the methods of preparing porous ceramics templates method, it is a new method to prepare porous ceramics with wood as a template. The porous ceramics obtained by this method are mainly wood ceramics and carbide ceramics with wood microstructure. The former is mainly a new type of porous carbon material made by high-temperature carbonization after impregnating wood or wood material with a thermosetting resin or liquefied wood. The latter uses charcoal as a template and is prepared by reactive melt siliconization, gas-phase reactive infiltration, and carbothermal reduction. The porosity ranges from 20 to 80 vol% according to wood types and preparation methods.
3. Biomimetic synthesis
Surfactants can self-assemble into liquid crystals and vesicles in water, which can be used as templates for biomimetic synthesis. Taney used a neutral surfactant with polar groups at both ends and a hydrophobic chain in the middle as a template molecule to form vesicles as a template and synthesized layered porous SiO2 with a pore size of 05~10mm. When the surfactant was in the water, it formed a spherical gel Spherical porous SiO2 can be synthesized when beaming.
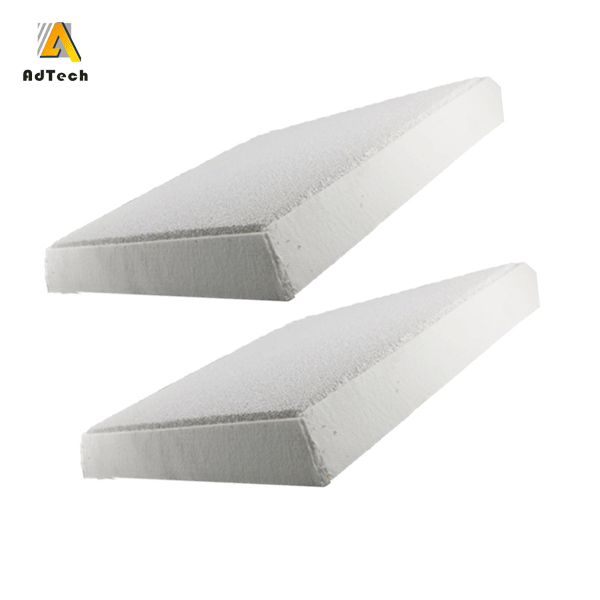
4. Hydrothermal-Heat Static Pressing
This process prepares porous ceramics with various pore sizes by using water as the pressure transmission medium. The preparation steps are as follows: the silica gel is mixed with 10wt% of water, placed in an autoclave, the pressure is 10-15MPa, and the temperature is 300°C. Porous ceramics are made by the volatilization of water vapor. In the hydrothermal-thermostatic pressing process, the reaction time is generally 10~180min, and the porous ceramics can be prepared under the condition of 25MPa for 60min. 30~50m, the compressive strength is as high as 80MPa. The porous ceramic hydrothermal-hydrostatic pressing process has the following advantages. The porous ceramic obtained has high compressive strength, stable performance, and wide pore size distribution.
In addition, there are some new preparation methods for ceramic foam filters for casting
such as mechanical stirring
In 1990, Fuji et al. invented a method for preparing ceramic foam filters for casting by generating foam with mechanical stirring. They added surfactant, methanol, and freon (foaming agent) to SiO2 sol (containing 40wt% silica, 0.4wt% soda) in turn, and then placed the mixture in a 30℃ water bath for 20~40mnin, when the mixture was When the viscosity rises to a certain level, stir the mixture to make the freon volatilize and foam. The foaming time is about one minute. After one minute, the foam volume will no longer increase. The foamed samples were stored in a water bath at 30 °C for 12 h, at room temperature for 6 days, placed at 700 °C for a week, then heated at 400 °C for 2 days, and fired at 100-1100 °C to obtain porous silica ceramics. Some scholars also use layered silicate as raw material, add 15~60w% binder, foaming agent, and filler to form a suspension, stir and inflate to form a wet foam material, dry the foam, and sinter at 1000~ ℃ to obtain Porous materials with a pore size of fewer than 60 μm, uniform pores, and compressive strength of 1.4 MPa.