porous ceramic filter slurry impregnation has strict requirements for the slurry. This article describes its impregnation process.
organic (polymer) foam impregnation
The organic foam dipping process was invented by Schwartzwalder in 1963. It is a method of impregnating ceramic slurry with organic foam and burning the organic foam after drying to obtain it. The good slurry is uniformly coated on the organic foam network, and the mesh-type pores are obtained after the organic foam is burned.
The pore size of the final product mainly depends on the pore size of the organic foam, and also has a certain relationship with the coating thickness of the slurry on the organic foam, but the pore structure of the mesh porous body is almost the same as that of the organic foam matrix. Pore three-dimensional network skeleton structure. The pore-forming principle of this process is shown in Figure 1-1
This special structure makes it significant advantages as a filter material: (1) When the fluid passes through, the pressure loss is small. (2) Large surface area and high fluid contact efficiency. (3) Lightweight. Compared with the traditionally used ceramic particle sintered body and glass fiber cloth, this kind of porous ceramic filter is used for fluid filtration, especially for molten metal filtration.
(1) It must be an open mesh material to ensure that the ceramic slurry can penetrate freely and adhere to each other so that a porous three-dimensional network skeleton can be formed after firing;
(2) It must have a certain degree of hydrophilicity, which can firmly adsorb the ceramic slurry
(3) There should be enough resilience to ensure that the excess slurry can be quickly rebounded and restored to shape;
(4) It volatilizes below the firing temperature of ceramics and does not pollute the ceramics.
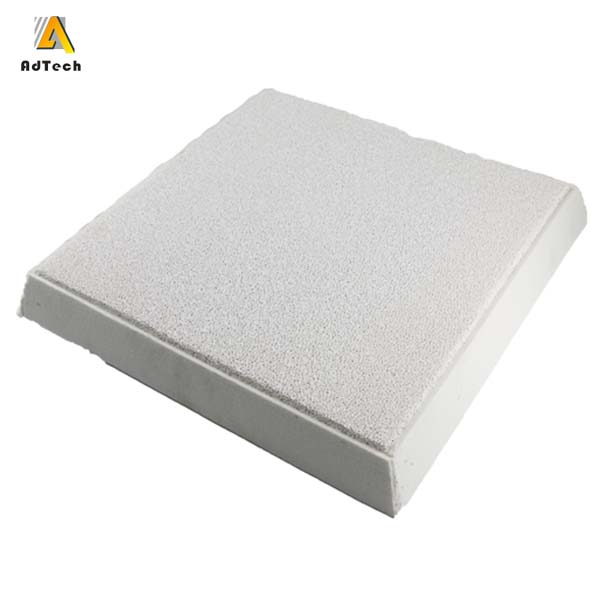
The ceramic powder is selected according to the different purposes of the porous ceramic filter slurry material developed. For example, to filter non-ferrous metals such as aluminum, copper, zinc, tin, and other low melting point alloys, cordierite, alumina, Al2O3, and Al2O3CrO3 series materials are generally selected; while smelting ferrous metals and their alloys, due to chemical activity and casting temperature higher.
The use of silicon carbide as a high-temperature filter; the use of partially stabilized zrO2-Al2O3 series materials and magnesium-aluminum series filter materials to filter molten steel can effectively reduce the content of inclusions in molten steel; the use of cordierite-mullite composite as ceramics The filter can filter diesel exhaust particles. In conclusion, the selection of suitable ceramic powders is very important for the preparation of high-performance and practical mesh porous ceramic filter materials.
The slurry is mainly composed of ceramic powder, solvent, and additives. Generally, water is used as a solvent, but organic solvents such as ethanol are also used. In addition to the properties of general ceramic slurry, the slurry also needs to have as high a solid content as possible (water content is generally 10~40wt%, slurry specific gravity is 18~2.2g/cm3) and better thixotropy. The high-performance slurry is not only beneficial to molding but also plays an important role in ensuring the performance of products. At the same time, to obtain a slurry that is more suitable for dip molding, a certain amount of additives must be added. The additives generally consist of the following:
(1) Binder. Adding a binder to the slurry for preparing mesh porous ceramic filter slurry not only helps to improve the strength of the green body after drying, but also prevents the green body from collapsing during the organic removal process, thereby ensuring that the final sintered body has sufficient mechanical strength. Binders are divided into inorganic binders and organic binders. Commonly used inorganic binders are potassium, sodium silicate, borate, phosphate, aluminum hydroxide sol, and silica sol. The type and characteristics of the binder have a great influence on the performance of the product. It is very important to choose the appropriate binder to improve the performance of the mesh. For example, porous alumina is prepared by using aluminum hydroxide gel as a binder, which greatly improves the corrosion resistance of the filter against molten aluminum.
(2) Dispersant. To increase the solid content of the slurry, dispersants need to be added to both water-based systems and non-water-based systems. Dispersants can improve the stability of the slurry, prevent the particles from re-agglomeration, and then increase the solid content of the slurry. However, it should be noted that for different powder systems, the effect of dispersants is generally different. For the water-based system of Al2O3, only 25wt% polyamine has a good dispersing effect; for the water-based system of SiC, PEI (polyethyleneimine) is ideal as the dispersant. In a word, choosing the appropriate dispersant is an important way to increase the solid content of the slurry.
(3) Rheology agent. According to the molding characteristics of this process, the slurry is required not only to have a certain fluidity, but also to have good thixotropy, that is, the slurry is required to be in a solidified state at rest, but recover fluidity under the action of external force. The flow properties of the slurry ensure that the slurry penetrates the organic foam during the impregnation process and is uniformly coated on the cell walls of the foam network. The thixotropy of the slurry can ensure that when the slurry is dipped and the excess slurry is extruded, the viscosity is reduced under the action of shearing, the fluidity of the slurry is improved, and it is helpful for molding. At the end of molding, the viscosity of the slurry increases. high, the liquidity is reduced. This makes the slurry attached to the hole wall easy to be rounded and shaped, to avoid the uniformity of the pores of the product due to the serious blocking of the green body due to the flow of the slurry. To improve the rheological properties of the slurry, especially the thixotropy, the rheological agents added are usually natural clays (0.1~12w%) such as bentonite, kaolin, and carboxymethyl cellulose.
(4) Surfactant. If the ceramic slurry is a water-based slurry, if the wettability between the organic foam precursor and the slurry is poor, a thick slurry will be attached to the intersecting part of the foam structure when the slurry is dipped, and in severe cases, it will lead to During the sintering process, the green body is cracked, and the strength of the porous ceramic filter slurry is obviously reduced or even collapsed. Therefore, the method of adding surfactant is usually used to improve the adhesion between ceramic slurry and organic foam to solve this problem, such as adding PEI (polyethyleneimine) and so on.
(5) Defoamer. To prevent the slurry from foaming during the process of dipping and extruding excess slurry and affecting the performance of the product, it is necessary to add a defoaming agent, generally low molecular weight alcohol or silicone. The organic foam must be repeatedly squeezed to remove air before impregnating the slurry, and then the slurry is impregnated. The methods include the atmospheric pressure adsorption method, vacuum adsorption method, machine maple rolling method, and manual rubbing method. No matter what method is used for impregnation, the slurry is required to be fully coated on organic foam. After the organic foam is impregnated with the slurry, the excess slurry needs to be removed. The key to this step is the uniformity of the extrusion force. It is necessary to remove the excess slurry and ensure that the slurry is evenly distributed on the network pore wall to prevent pore blocking. . The bulk density of the formed green body is suitable in the range of 04~0.8g/cm3. Large-scale production should be completed with equipment such as centrifuges or rolling mills.
The green body obtained by extruding the excess slurry needs to be dried and can be dried in the shade, oven-dried, or microwave oven-dried. When the moisture content is below 1.0wt%, it can be fired. To shorten the production cycle, it is generally required to formulate a reasonable drying system.