Cordierite porous ceramic filter boards. Advanced materials study methods ( DSC and XRD ) were applied in this research to study the properties of the porous ceramic filtration boards sy stem atically. The porosity of the Al O3 and Cordierite porous ceramic was also tested. The influence of the Ceo addition on the transformation in interprocess, the sintering property, and the mechanical performance of the cordierite ceramicware was also determined. This work is of significance and importance to prepare porous ceramic with high porosity and high mechanical performance, regulate the relationship between porosity and strength, moreover, to exploit new porous ceramic materials was shown in the result that the polymeric sponge impregnation procedure is an ideal process for preparing porous ceramics, with its simplicity and cheapness. In the preparation, the properties of the final products were affected by the selection of polyurethane, the sintering temperature, and the holding time. It can also be found that along with the porosity increasing, the compression and flexural strength decreaseAccordinglyThe main phase of the Al, O3 Cordierite porous ceramic filter is corundum. Take the pore size of3oppi as an example, the compression and flexural strength of the Al2 O3 porous ceramic filter whose porosity is 88.9 vol 3.31 Mpa, and 1.69 Mpa. And, the compressicflexural strength of the Al2 O3 porous ceramic reach to 3.50 Mpa and 1.91 Mpa, when the porosity is 86.8 vol %. The Al2 O3 porous ceramic is of high thermal shock resistance mam phase the cordierite porous ceramic is cordierite. After adding Ceo2when the pore size is 30ppi, the average compression, and flexural strength rise from4. 01MPA and 2. 03MPA20MPA and 2. 10MPA is excellent thermal shock resistance.
Keywords: Cordierite porous ceramic filter, cordierite, Al2o 3 Ceo porosity mechanical properties
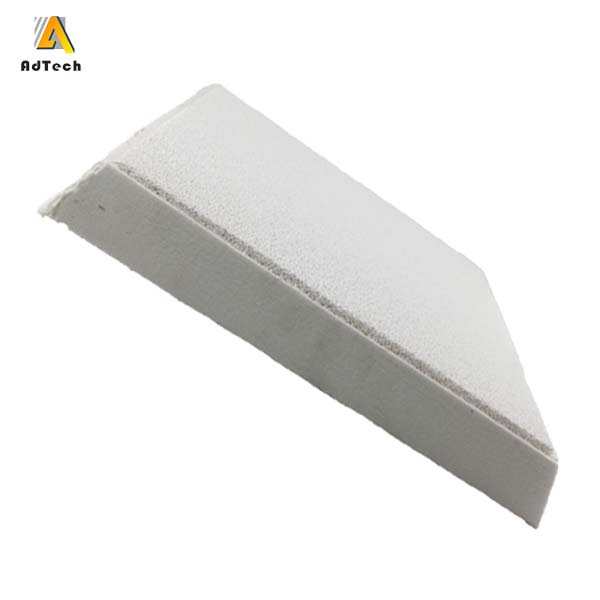
porous ceramic filter overview porous ceramic filters can be divided into foam ceramics and honeycomb ceramics according to the shape of the pores. Foam ceramics is a kind of ceramic product with uniform distribution of micropores (porosity can be as high as 50~90vo1%), low bulk density, three-dimensional network skeleton structure, and interconnected ceramic products①. It has developed specific surface area and unique physical surface characteristics, selective permeability, energy absorption or pressure resistance characteristics for liquid and gas media, and has the unique high-temperature resistance, corrosion resistance, and thermal stability of ceramic materials. Outstanding feature
1.1.1 Classification of Cordierite porous ceramic filter Materials
porous ceramic filters that have been developed at present are divided into the following categories. The relationship between pores can be divided into closed pores and open pores. Closed pores refer to the internal micropores of the ceramic material distributed in the continuous ceramic matrix, and the pores are isolated from each other, and the open pores include the interconnection between the internal pores and the pores of the material, and the two sides that are open on one side and closed on the other side to form non-connected pores. kind. According to its pore size, it can be generally divided into the microporous ceramic filter (pore size less than 20A) meso porous ceramic filter (pore size range of 20~500A), and Cordierite porous ceramic filters (pore size greater than 500A).
According to their different materials, they can be divided into ① high siliceous silicate materials: hard ceramic slag, acid-resistant ceramic slag and other acid-resistant synthetic ceramic particles are used as aggregates, which have water resistance and acid resistance, and the operating temperature reaches ② Aluminosilicate materials: with refractory clay clinker, sintered bauxite, sillimanite and synthetic mullite particles as aggregates, it has acid resistance and weak acid resistance, and the service temperature can reach 1000 ℃; ③ static ceramic materials: The composition is close to the first material to obtain microporous ceramic materials by mixing a variety of clay clinker particles with clay; ④Diatomite material: It is mainly made of selected diatomite as raw material and sintered with clay, which is used for fine filtration of water and acidic medium; ⑤Pure carbonaceous material: made of low ash coal or petroleum pitch coke particles, or adding part of graphite, and bonding and firing with dilute tar, it is used for water resistance, hot and cold strong acid, cold and hot strong alkali medium and air Disinfection, filtration, etc.; ⑥ Corundum and emery materials: Different types of fused corundum and silicon carbide particles are used as aggregates, which have strong acid resistance and high temperature resistance, and the temperature resistance can reach 1600 ° C: ⑦ Cordierite, aluminum titanate materials: because of The thermal expansion coefficient is small and is widely used in thermal shock environments; ⑧ other industrial wastes, tailings and materials composed of quartz glass or ordinary glass are used in different fields depending on the composition of raw materials.