Abstract: The online degassing process(degassing unit) is studied, and according to the characteristics of several kinds of aluminum and aluminum alloy online degassing processes and equipment that are commonly used at present, the box-type degasser, launder-type degasser, and vacuum degasser are described in detail. The structural characteristics and other notable features of these typical aluminum and aluminum alloy online degassers, introduce the new development of online degassing unit technology-ultrasonic degasser and comprehensively evaluate these typical aluminum and aluminum alloy online degassers The advantages and disadvantages of the aluminum melt casting workshop will help to choose the appropriate degassing process and equipment to improve the quality of aluminum and aluminum alloys.
Keywords: aluminum melt; online refining degassing process; advantages and disadvantages
There are many factors that affect the quality of aluminum and its alloys, among which the hydrogen content, inclusions, and alkali metal concentration of molten aluminum are the most important for the quality of aluminum alloys. Major manufacturers and research institutions at home and abroad have invested a lot of resources in research on how to reduce the hydrogen content and inclusion content in molten aluminum, and many new processes and equipment have appeared on the market.
1. On-line degassing process
The online degassing process can be roughly divided into gas blowing method, vacuum refining method, and ultrasonic refining method. This article focuses on the gas-blowing method.
1.1 Principle of gas blowing method
The gas-blowing method, also known as the flotation method, is mainly to form many tiny bubbles after blowing inert gas into the molten aluminum. The initial pressure of hydrogen in the bubble is zero, and there is a pressure difference of hydrogen at the interface between the bubble and the aluminum liquid so that the hydrogen dissolved in the aluminum liquid is continuously sucked into the bubble. This suction process is until the pressure of the hydrogen in the bubble and the aluminum liquid will stop when the pressure of hydrogen in the medium is equal. After the bubbles surfaced, the hydrogen in the bubbles escaped and entered the atmosphere.
The schematic diagram of the hydrogen removal principle is shown in Fig. 1.
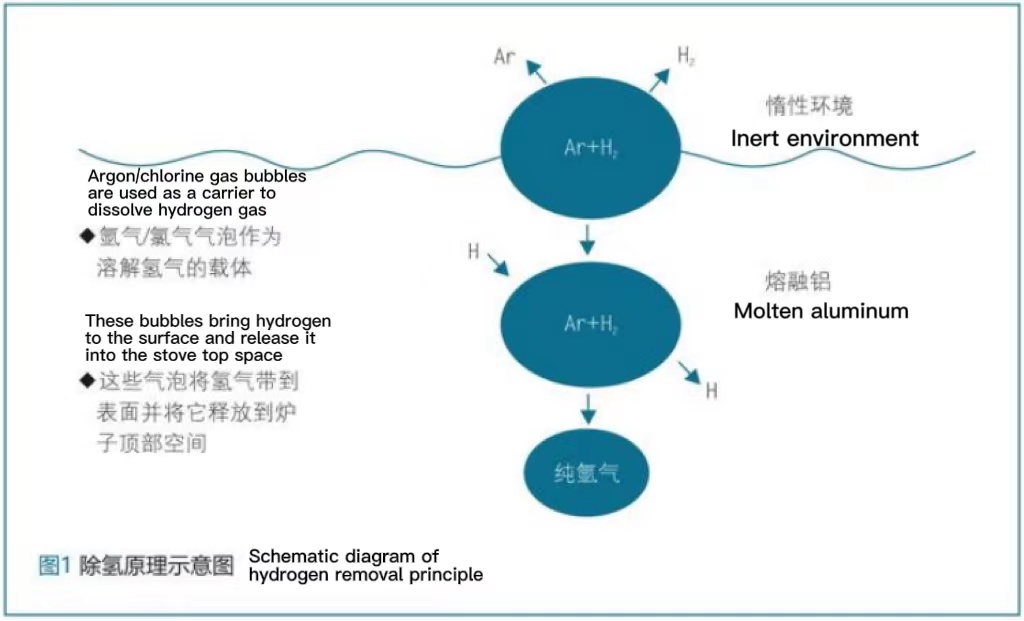
In addition, when the bubbles pass through the melt, they meet the oxide inclusions in the melt, and the inclusions are adsorbed on the surface of the bubbles and float up to the surface of the melt with the bubbles to be removed. The schematic diagram of the removal of inclusions is shown in Fig. 2.
Therefore, the rising process of the bubbles can not only bring out hydrogen to achieve the effect of degassing but also bring out oxidation inclusions to achieve the effect of refining.
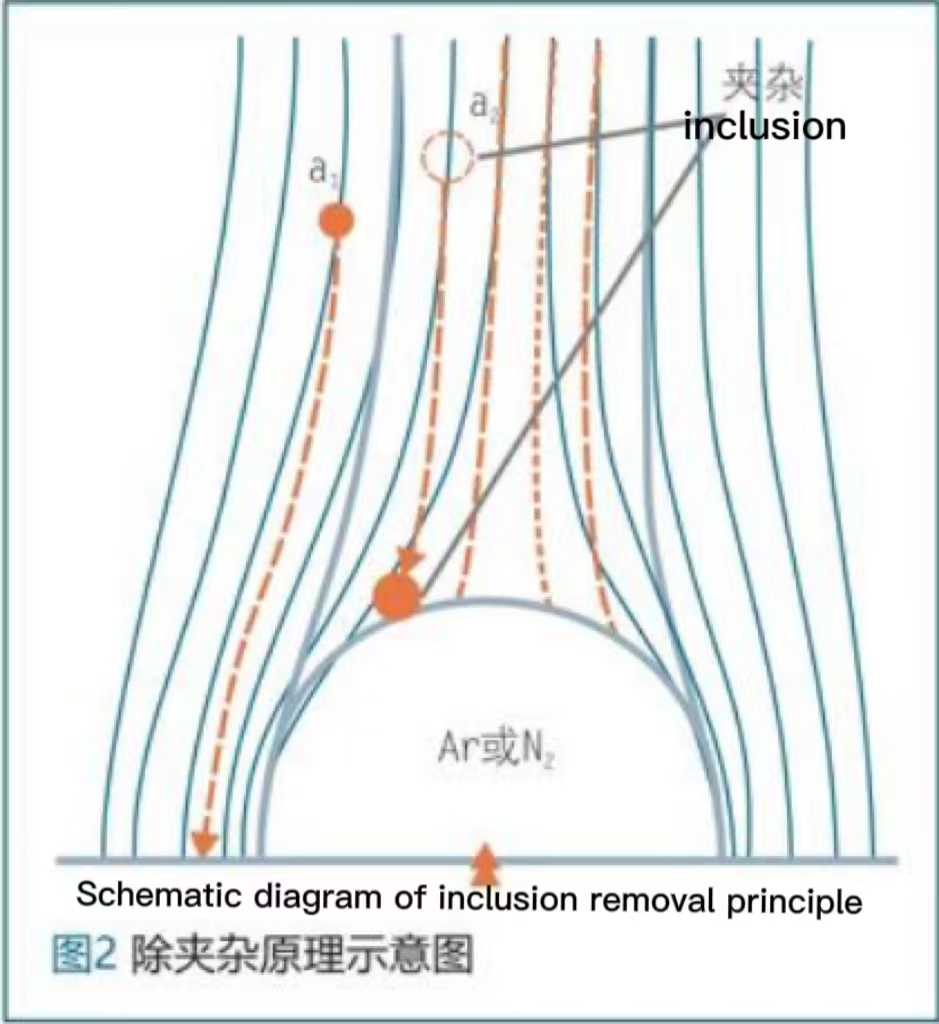
1.2 Inert gas feeding method
In the gas-blowing method, the way of introducing inert gas into the molten aluminum has a great influence on the effect of degassing and refining. At present, there are three commonly used methods for introducing inert gas into molten aluminum in casting plants, including degassing pipes, venting bricks, and rotating degassing units, as shown in Figure 3.
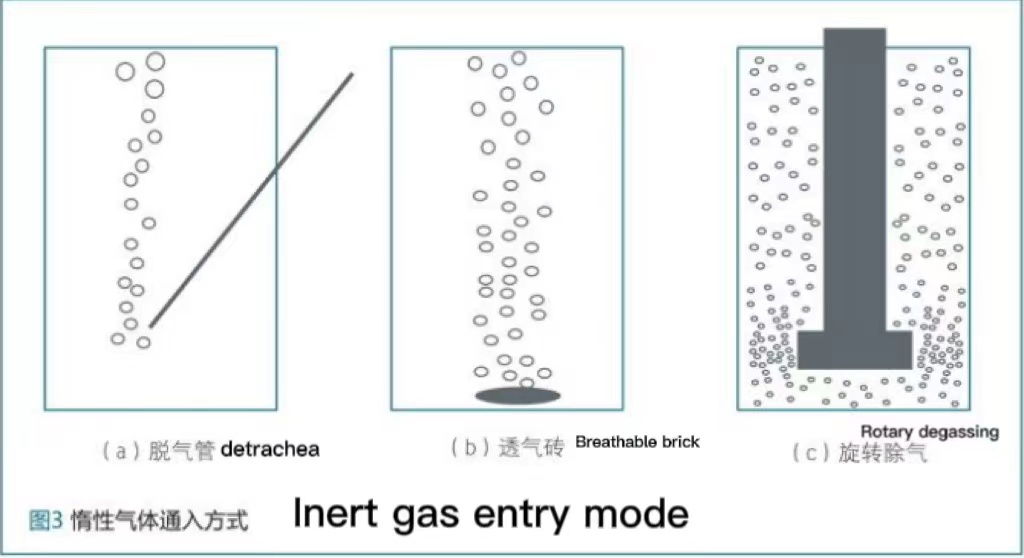
The simplest method of the gas blowing method is to insert a refining tube (usually an enamel steel tube) into the molten aluminum, and then pass in an inert gas. This single-hole single-tube degassing method has a poor degassing effect. There are also some casting factories that install breathable bricks at the bottom of the furnace. The inert gas passes through the breathable bricks to form multiple bubbles. Compared with the single-hole blowing method, the degassing and refining effect of the porous blowing method is slightly better; Bricks have disadvantages such as easy blockage, aluminum liquid leakage, difficult maintenance, serious liquid surface tumbling, and more slag formation.
With the deepening of research, the rotary degassing method has appeared one after another. The basic principle is that the inert gas is sprayed into the molten aluminum through the rotating rotor to form a large number of dispersed small bubbles, thereby performing degassing and refining treatment. In order to improve the degassing efficiency, the number of inert gas bubbles should be as large as possible, the diameter of the inert gas bubbles should be small, the residence time of the inert gas bubbles in the aluminum liquid should be long, and the aluminum liquid surface should be as stable as possible.
In order to achieve the above purpose, each degasser manufacturer has its own characteristics in the design of the rotor/rotary rod, the inner lining of the box, and the sealing method of the box, thus forming various types of degassers currently on the market. According to the degassing process and structural characteristics of the degasser, it can be roughly divided into box-type degasser, launder-type degasser, vacuum degasser, and ultrasonic degasser.
According to incomplete statistics, 99% of the online degassers currently on the market are box-type rotary degassers. The box-type degassers include SNIF and ILDU degassers from PYROTEK in the United States, Reveot degassers from Apogee in the United States, APLUR degassers from Novelis in France, Fujiko GBF degassers in Japan, and Mitsui (Japan) degassers. TKR) degasser, Alcoa (Alcoa) 622 degasser are the most typical; launder type degasser is the most typical ACD degasser produced by Canada STAS company; vacuum degasser is Hycast produced by Hydro. I-60Sir is the most typical.
In recent years, Southwire Co., Ltd. (Southwire) in the United States has newly developed an ultrasonic degasser.
2. On-line degassing unit
2.1 Box degasser
The structure of the SNIF box-type degasser produced by American Pilotec is shown in Figure 4.
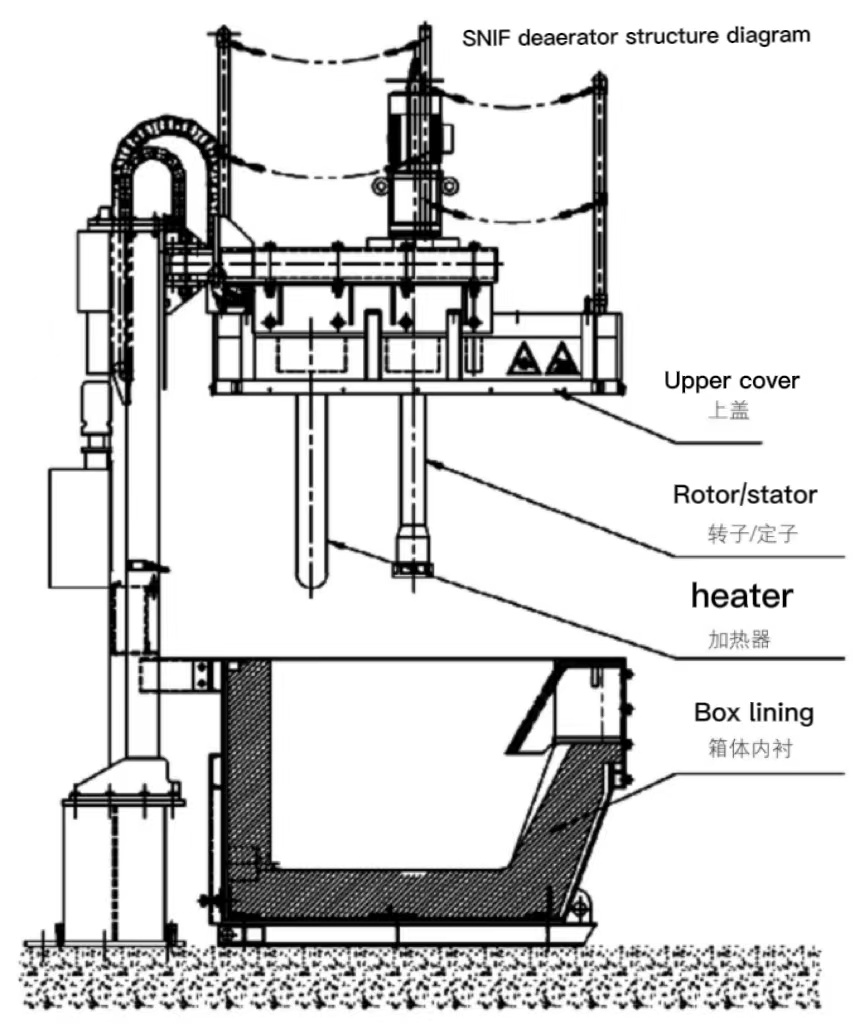
The molten aluminum flows into the degasser box and stays in the refractory lining. The box has a heater to keep the molten aluminum in a molten state. After the inert gas is sprayed out by the rotating rotor, it is broken into countless small bubbles by the high-speed rotating rotor, and the small bubbles diffuse and rise in the aluminum liquid, thereby removing hydrogen. During the rising process of the small bubbles, due to the effect of surface tension, a part of the inclusions will be taken out from the molten aluminum to the liquid surface, forming scum to remove the inclusions in the molten aluminum; at the same time, through the agitation of the rotor, the liquid aluminum will The composition of the alloy is more uniform.
The most notable feature of the box-type degasser is the graphite stator and graphite rotor/rotor structure. The graphite stator does not rotate in the aluminum liquid and acts as an outer layer protection for the graphite rotor/rotor assembly. Graphite rods and graphite rotors are assembled together to stir the aluminum water. The inert gas passes through the gap between the stator and the graphite rod and is sprayed into the molten aluminum from the bottom edge of the stator and the groove on the top edge of the graphite rotor. SNIF graphite rod/rotor aluminum liquid circulation mode is shown in Fig. 5.
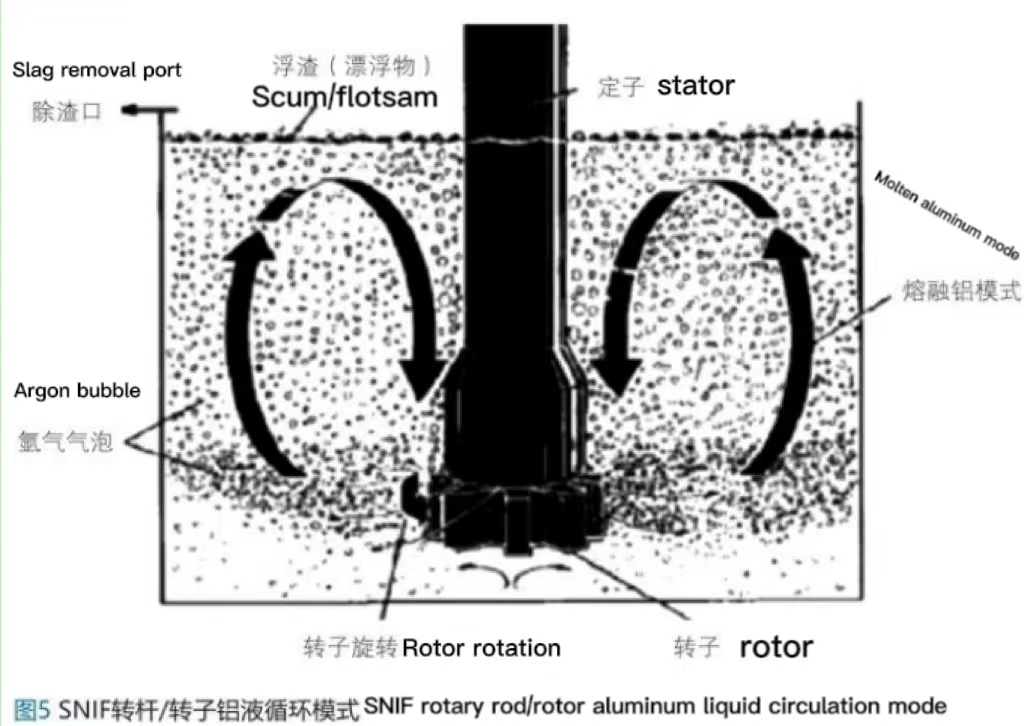
Through the shear force of the graphite rotor, the molten aluminum is circulated downward, thereby offsetting the influence of natural buoyancy, so that the air bubbles ejected from the rotor and stator are radially injected and evenly dispersed in the molten aluminum to achieve the best degassing Refining effect. In another series of ILDU box-type degassers produced by American Parrotec, the remarkable feature is the rotating rod/rotor (see Figure 6).
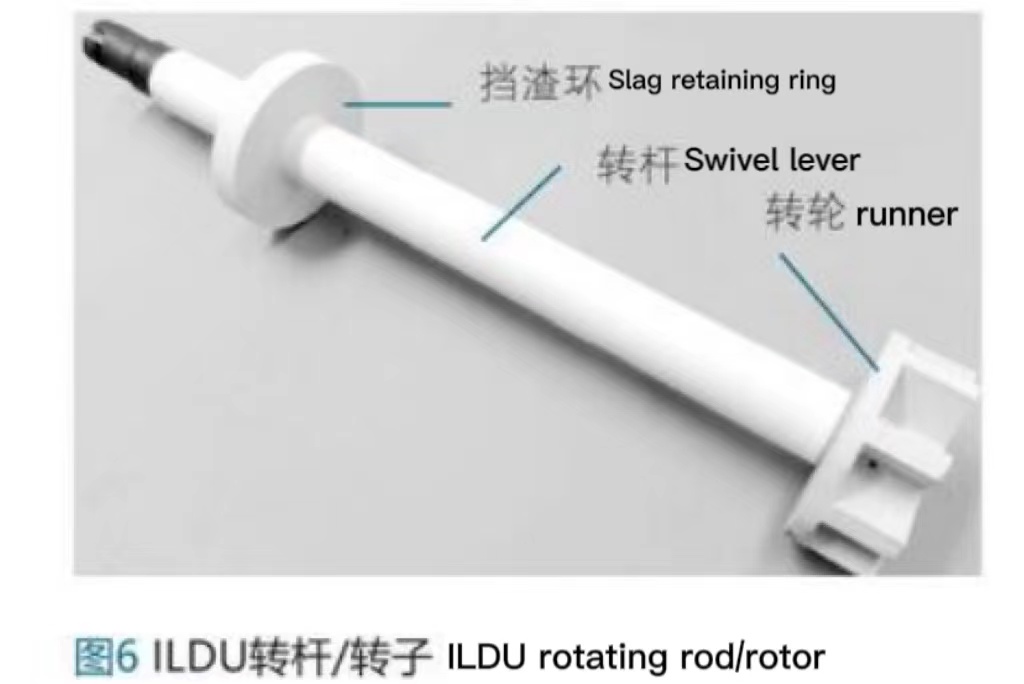
The material of the rotating rod/rotor is the new BTS. At present, the materials of other degasser rotors/rotors are generally graphite, silicon carbide, and silicon nitride. Graphite is easy to burn and oxidize at high temperatures (about 750°C), causing fracture or peeling, thereby contaminating the aluminum liquid; the silicon carbide casting rotor is not resistant to thermal shock, and is easy to break under rapid cooling and thermal shock; silicon nitride rotating rod/ The rotor cost is too high. However, the inside of the BST rotor/rotor is made of graphite material and the outside is sintered with refractory material, which just overcomes the shortcomings of the above three materials. According to statistics, its service life is as high as more than 1 year on the continuous casting and rolling line.
The obvious advantages of the box-type degasser are as follows: 1) Increase the residence time of the bubbles, thereby improving the degassing and refining effect; 2) Keep the temperature of the molten aluminum in the box equal to or higher than the casting temperature, thus reducing the temperature of the holding furnace. temperature; 3) reduces the change of casting temperature. The disadvantage is that the installation space required for the device is relatively large.
2.2 Launder-type degasser
The trough-type degasser uses the rotor/rod to rotate the degasser and refine it. The main difference in structure between the launder-type degasser and the box-type degasser is that the inner substrate of the launder degasser is flush with the inner substrate of the launder on the casting production line, thus realizing The degasser has no residual aluminum. The structure diagram of the launder-type degasser is shown in Fig. 7.
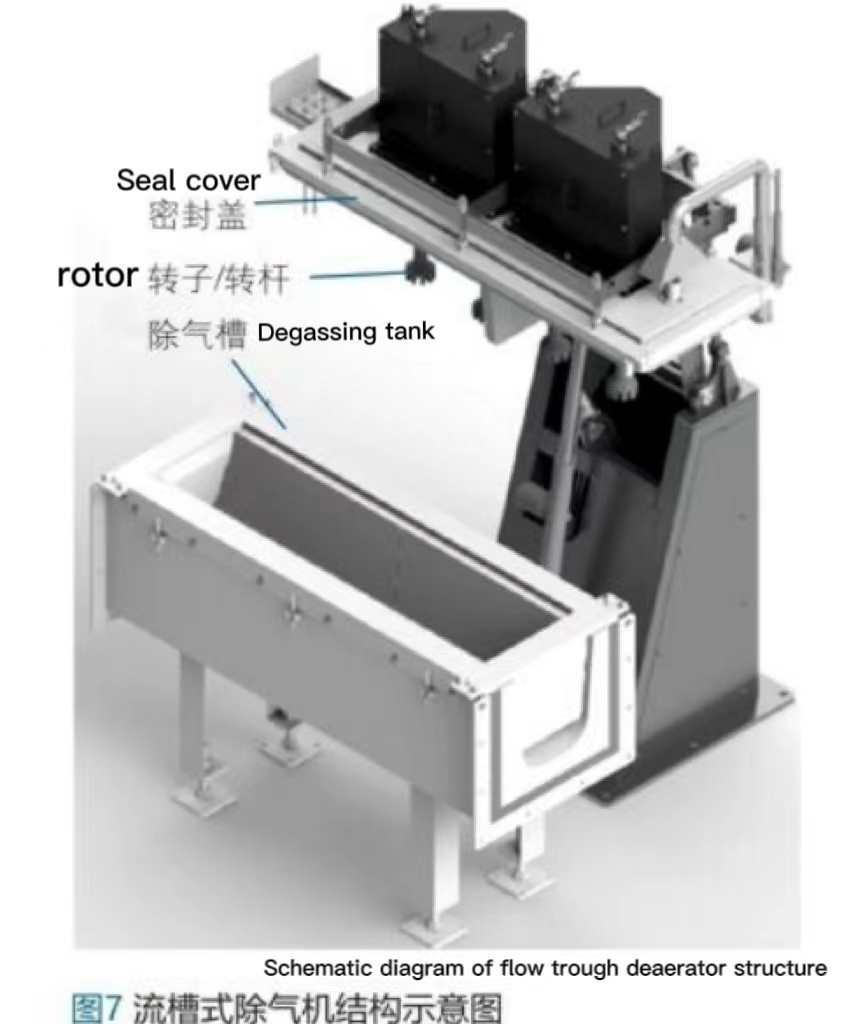
The sealing cover and the degassing tank of the launder-type degasser form a relatively sealed space. When starting the casting, the molten aluminum enters the degassing tank through a submerged flow. When the aluminum liquid level in the degassing tank is higher than 200mm, the rotor starts to stir the aluminum liquid and sprays inert gas into the aluminum liquid to degas and refine the aluminum liquid in the degassing tank. Compared with the traditional box-type degasser, the trough-type degasser has the advantages of no residual aluminum and a small footprint. Its disadvantages are also obvious: due to the shallower aluminum liquid depth of the launder-type degasser, the residence time of the bubbles in the aluminum liquid is shorter, so its degassing effect is slightly lower than that of the box-type degasser. Since there is no heating system, the temperature of molten aluminum will decrease (usually by 10-35°C) when it passes through the degassing unit, which will affect the subsequent casting process.
The speed of the graphite rod/rotor of the launder-type degasser is very high (>1000r/min), so the service life of the graphite rod/rotor is short and more slag is produced. Because the bubbles stay in the molten aluminum for a short time, which affects the degassing effect, the operator generally counteracts this adverse effect by increasing the flow rate of the inert gas, which leads to large consumption of the inert gas.
(porous ceramic filter)
2.3 Vacuum degasser
The structure of the vacuum degasser is similar to that of the launder-type degasser, which is divided into two parts: the degassing unit and the vacuum degassing chamber (see Figure 8).
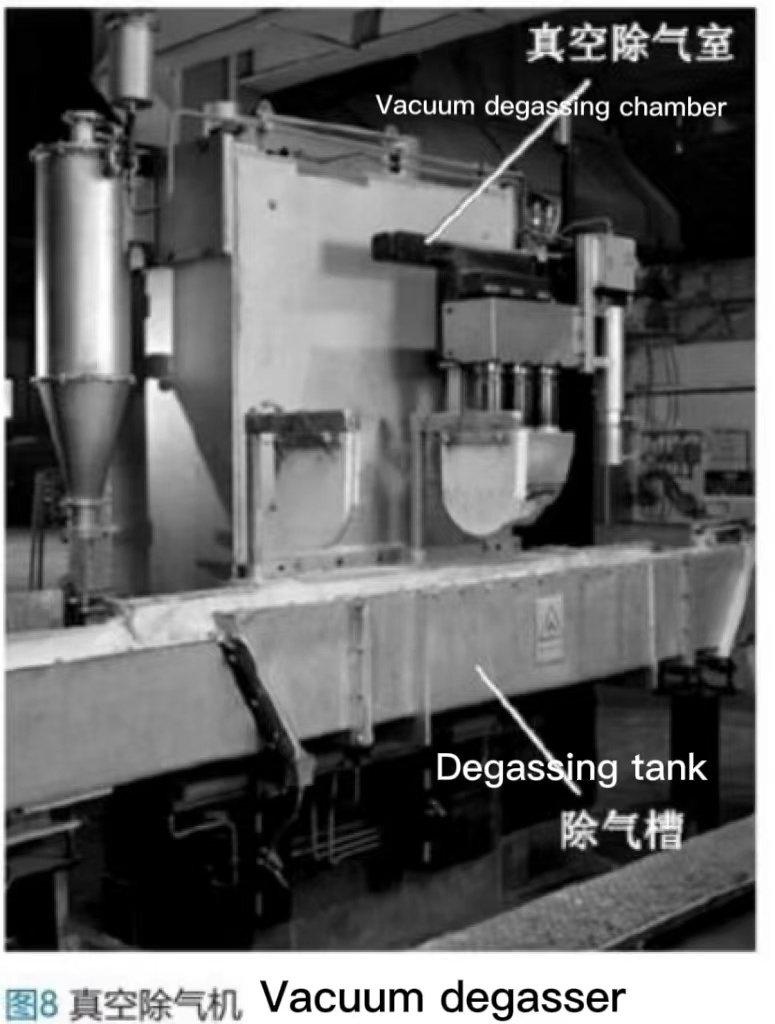
The vacuum degassing chamber can be divided into a single chamber, double chamber, and multi-chamber according to the flow rate of aluminum liquid. The difference between the box-type and launder-type degassers is that the graphite rotor of the vacuum degasser is installed at the bottom of the degassing chamber. The bottom of the degassing chamber is slotted so that the vacuum degassing chamber communicates with the degassing unit (see Figure 9). When the molten aluminum flows through the degassing unit, the degassing chamber forms a negative pressure under the action of a vacuum pump or other methods, thereby increasing the liquid level of the aluminum liquid in the vacuum degassing chamber. After the aluminum liquid level reaches a certain height, the graphite rotor starts to rotate and inject inert gas to degas and refine the aluminum liquid. When the degassing is over, the negative pressure in the vacuum chamber is released, and the liquid level of the aluminum liquid in the vacuum chamber drops until it is equal to the liquid level of the degassing unit.
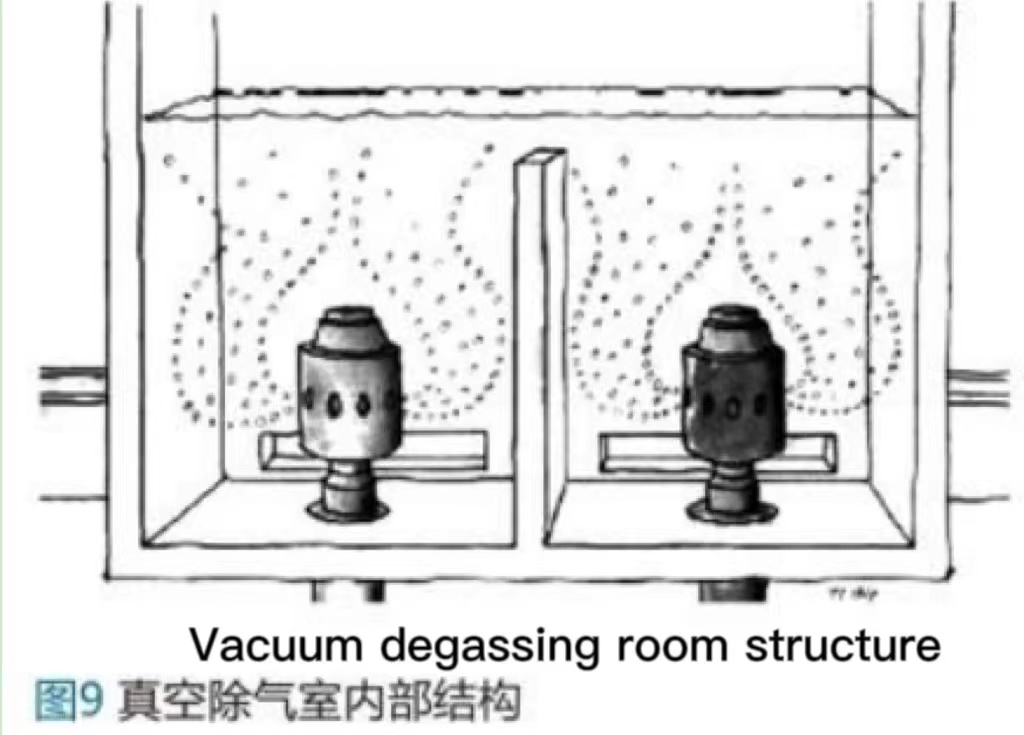
The vacuum degasser has the advantages of no residual aluminum and a small footprint. In addition, since the aluminum liquid is degassed and stirred in a vacuum state, there are fewer oxides and the aluminum liquid is relatively clean. Disadvantages of the vacuum degasser: 1) High requirements on the cleanliness of the aluminum liquid; 2) Since the graphite rotor is installed at the bottom, and there is more slag at the bottom of the aluminum liquid, the graphite rotor is easy to wear. At present, vacuum degassers are not widely used in the market.
2.4 Ultrasonic degasser
The ultrasonic degasser is a new type of degasser successfully developed by South Line Co., Ltd. in the United States. The ultrasonic degasser is different from the traditional rotor-rotating degasser, its structure includes an ultrasonic transmitter and its ultrasonic probe (see Figure 10).
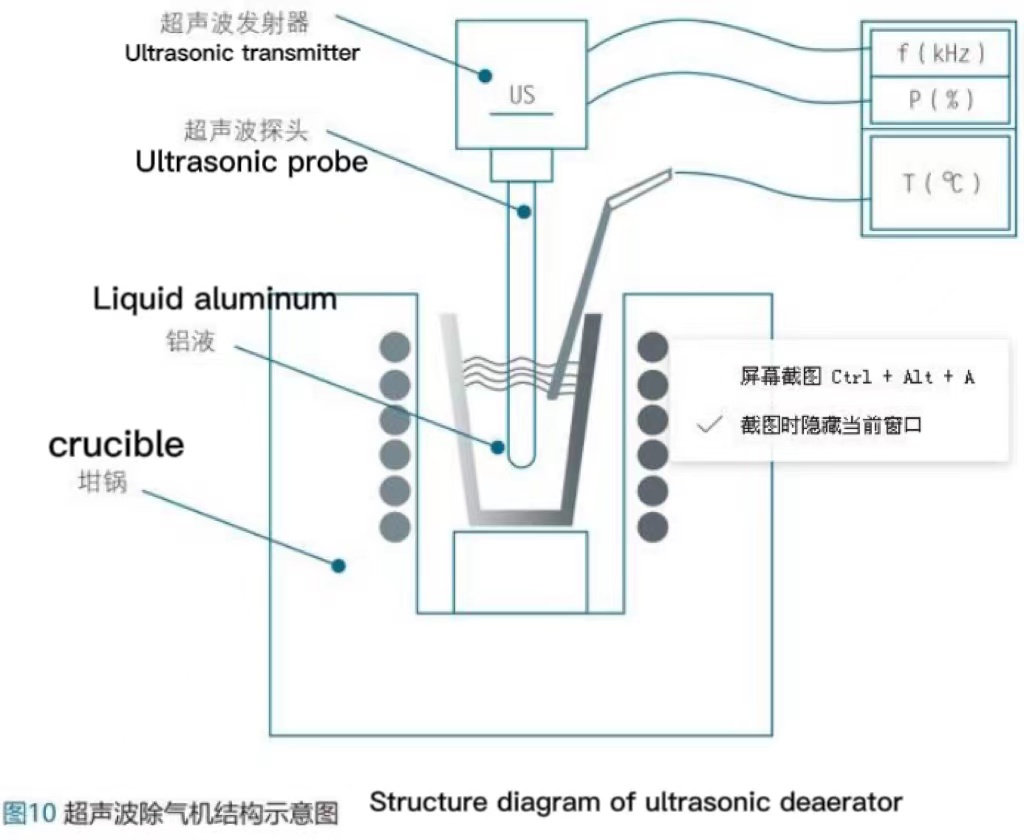