Aluminum degassing machine uses an inert gas to remove hydrogen from molten aluminium. Nowadays, the aluminium industry requires strict metal quality standards, so as to improve metal quality and prevent part failures in critical components of automobiles, airplanes and machinery. Inclusions can lead to reduced fluidity, increased porosity, loss of mechanical properties, poor surface finish, lack of pressure tightness and reduced corrosion resistance.
The larger surface area increases the rate of transfer from metal to the inert gas. The smaller the bubble size for a given volume of gas, the greater is the surface area. For example, a 1” diameter bubble of gas has a surface area of 6 square inches. If the same bubble divides into 1/16” diameter bubbles, the surface area increases to 96 square inches. In other words, if the same volume of gas is used and the diameter of the bubbles reduce to 1/16th the original diameter, the total surface area increases by a factor of 16. The smaller bubbles disturb the surface of the melt less reducing additional hydrogen pickup from humid atmospheres.
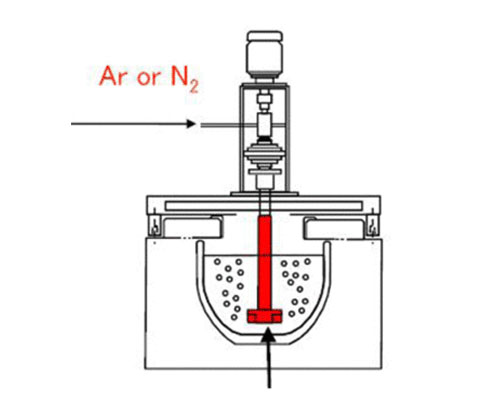
Aluminum Degassing Machine
- Optimal process gas bubble dispersion throughout the melt
- Reduce dross formation
- Increase metal quality
- Expert engineering design
- Recommended for dry nitrogen or argon
In production, in order to quickly detect the hydrogen removal effect of aluminum melt, the density index comparison method is usually used. That is, the density ρ1 of the sample solidified by aluminum under vacuum and the density ρ2 of the sample solidified in the air are taken out separately. Density index = (1-ρ1/ ρ2) × 100. Generally, liquid aluminum is qualified under this situation: the density index of aluminum liquid in pressure casting is less than 1.5. The density index under low-pressure casting and gravity casting is less than 1.
(1) The more and finer the argon bubbles, the larger the contact area of the aluminum liquid with the bubbles. The shorter the diffusion distance of hydrogen atoms in the aluminum liquid, the longer the bubbles stay in the aluminum liquid, and the better the degassing effect.
(2) During the refining process, the graphite nozzle rotates and sprays at the bottom of the aluminum liquid. On the one hand, it promotes the accumulation of small inclusions in the aluminum liquid in the transfer bag. On the other hand, the surface of the aluminum liquid is always stable. There is no violent tumbling phenomenon, which avoids the mixing of oxygen, reduces the generation of oxide inclusions and the secondary dissolution of hydrogen.
(3) Ar is an inert gas, non-toxic, odorless, pollution-free. Ar dehydrogenation mainly plays a role in the physical dehydrogenation of aluminum melt. The scum formed is brought out of the bubble from the aluminum liquid. Compared with flux purification, the amount of slag formed is small, and no toxic gas is generated. The rotary degassing system greatly improves the working environment and reduces the harm to the environment.
Pingback:Degassing Device,Molten Aluminum Degassing Unit,Aluminum Degasser
Pingback:Define Degassing,Aluminum Liquid Purification Device
Pingback:Main Components of Degassing Device – 站点标题
Pingback:Molten Aluminium Define Degassing – 站点标题